Some like it cold.
You've met your makers in the hot shop, but our craft is more than just a bunch of hot air. The cold shop is where many of the details of our lighting are crafted and created.
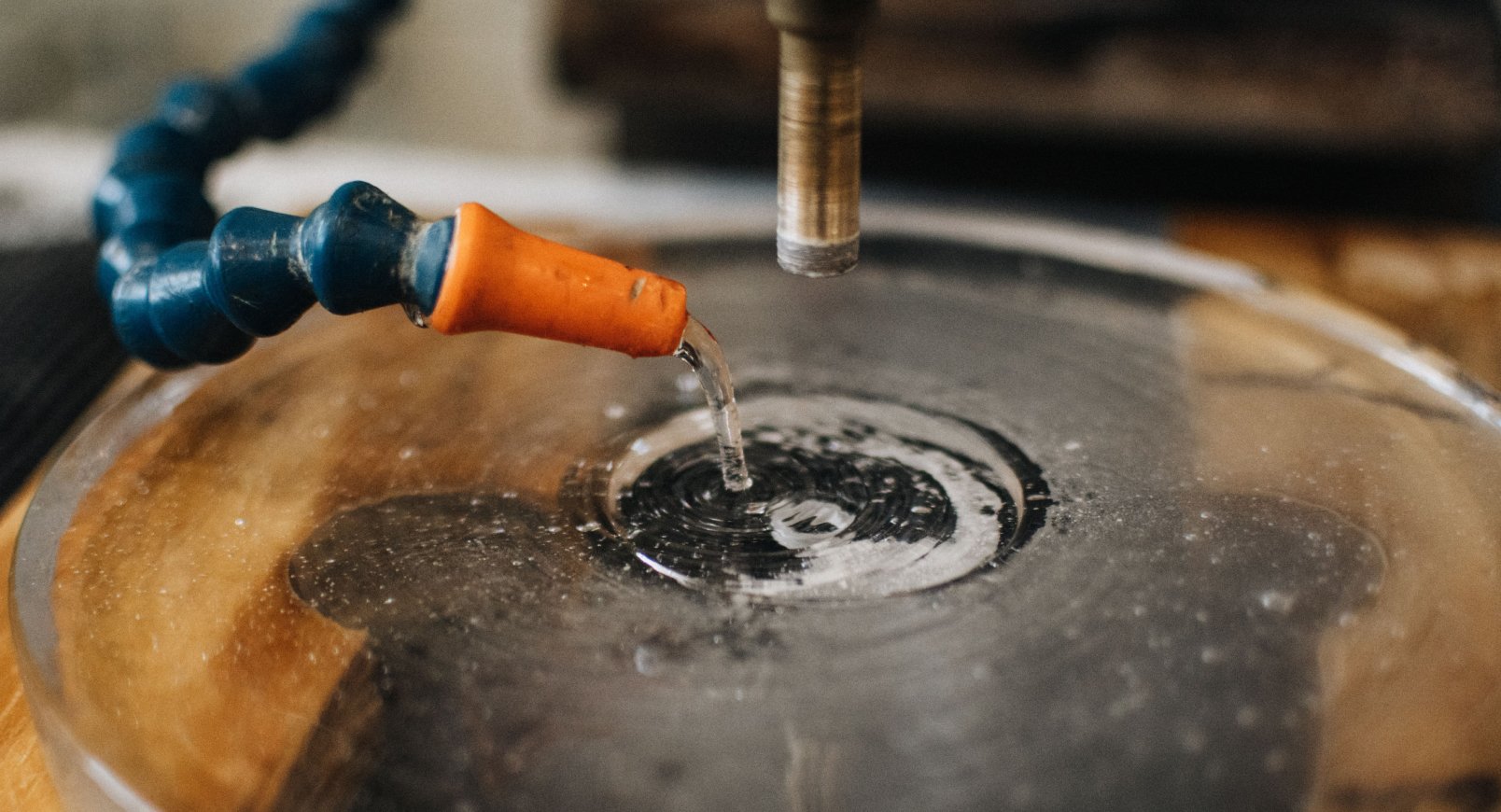
What happens in the cold shop.
Outside of using a small torch to "clip" or "hot-pop" glass, there are no processes or tools that transfer of from working molten glass in the hot shop to finishing glass in the cold shop.
The processes in the cold shop include cutting, via torch (when"clipping" or "hot-popping") or using a wet diamond saw.
Drilling is possible on a drill press, using diamond coated core bits that are cooled with water while in use. Most all of our products go through the drilling process to create the opening for the light module to attach to.
Grinding is done one of two ways. 1. By using a lap wheel. A lap wheel consists of a large, 2" thick steel disc that is attached to an electric motor and spun. As the disc or "head" of the wheel spins, a slurry of grit (silicon carbide + water) drips onto the wheel. The glass is very carefully lower to the head of wheel and held level while the material is ground away by the grit.
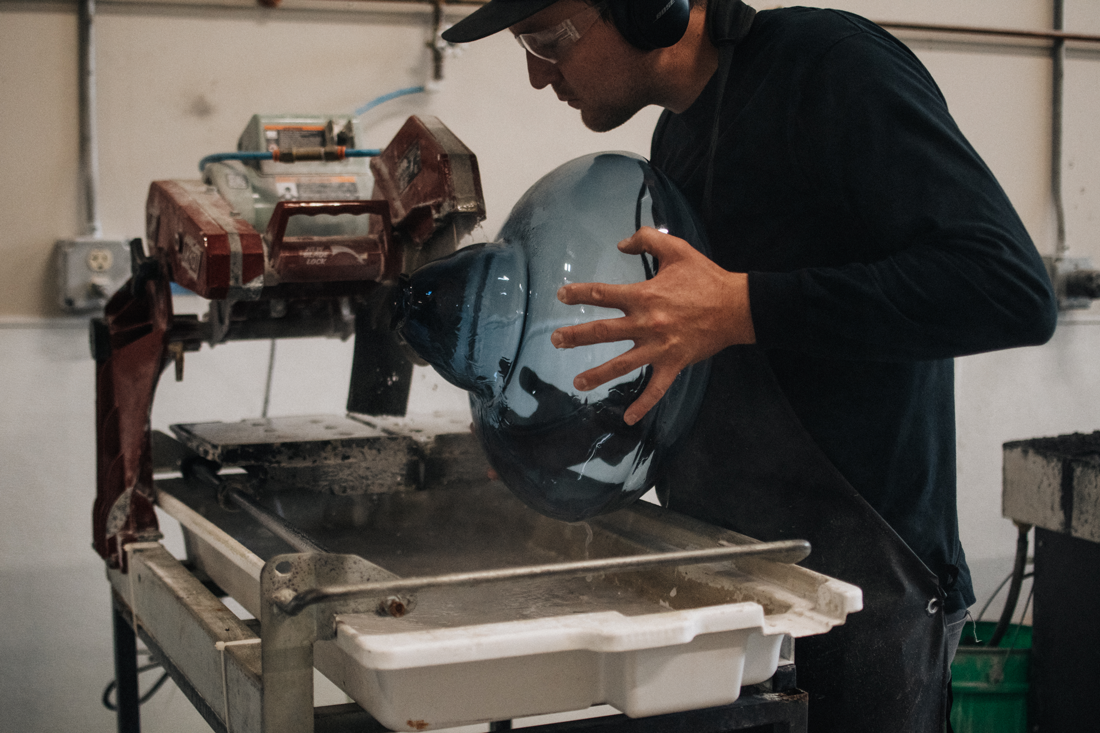
Water works.
Most equipment in the cold shop is cooled by water spaying on them during use. This includes the vertical sanding belt, which uses a variety of grit textures to achieve the polish of the glass. The sanding belt also is used to bevel the glass and create the exterior "lip" that creates an opening to the vessel.
Don't judge a cold shop by its cover.
The cold shop is a challenging part of our production process to romanticize. Cold shops typically aren't the most photogenic of spaces to photograph, and our cold shop is no exception to that rule. The equipment is largely adapted from it's intended function to work as glass working equipment. While the functional result is what we need, the equipment itself often looks "DIY" and doesn't necessarily match the highly polished aesthetic of our finished designs.
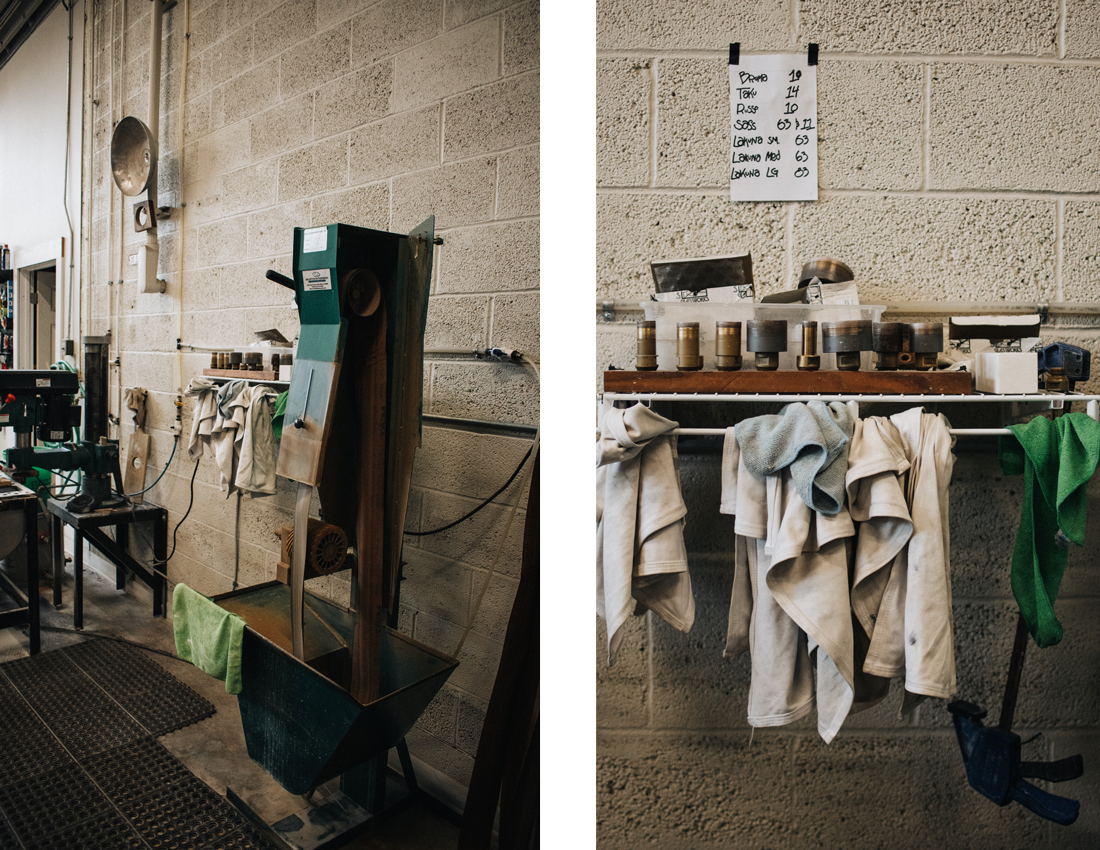
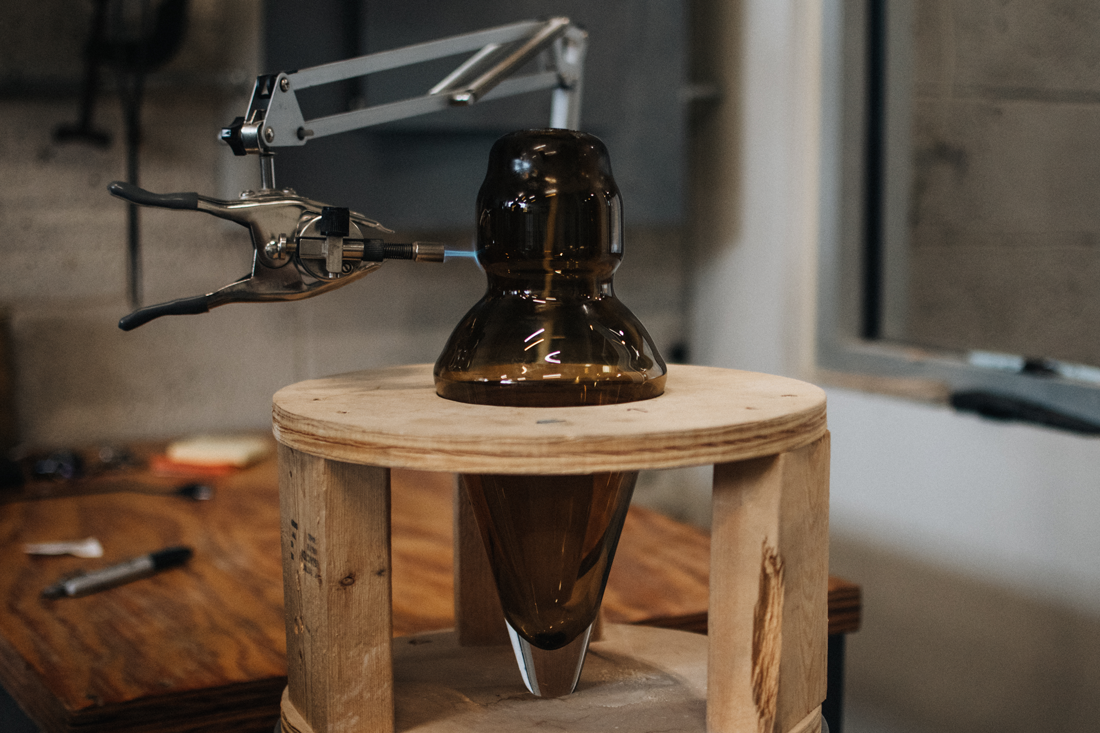
.png?v=1684811647176)
